Compact grading line for seed potatoes commissioned at Geerligs in Anna Paulowna
DT Dijkstra recently commissioned a compact seed potato grading line at the farm of Geerligs in Anna Paulowna.
This line was supplied by Prinsen Agricultural & Handling Solutions of Emmeloord.
Intensive and optimal collaboration has resulted in a bunker installation with a compact build, entirely in line with the customer’s requirements.
The Geerligs partnership excists of the brothers Dirk and Henk Geerligs.
In addition to sugar beet, cereals and grass seed, they also cultivate 50 hectares of seed potatoes.
The business also has its own storage facility.
During the winter period, the brothers grade and inspect the seed potatoes and pack them into boxes, bags or big bags, ready for delivery or on-site use.
‘We have been grading with a DT Dijkstra AT2/5 machine for many years’, says Henk Geerligs.
‘This machine is very reliable, with low operating costs, but the old installation took up a lot of space in the barn because all the components were installed in line, one behind the other.
We have already invested in an automated Van Hees Machinery box filling and emptying module with a stacker and destacker, which we also wanted to use for grading.
Other modules have also been added, such as a bag-sewing station and a palletising machine.
All in all, the set-up of the grading installation no longer suited our requirements’.
Effective
The combination of the DT Dijkstra bunker installation and the VHM box filling and emptying module with box warehouse makes for a highly effective installation.
Henk explains: ‘We can buffer a large volume of product before and after grading. As a result, with one person working in the inspection room and the other taking care of product feeding and discharge, my brother and I can grade all batches ourselves’.
Dust prevention
The recently commissioned installation was constructed in an area of 5.5 x 15 m.
This area is surrounded by walls so that it is separated from the processing area.
‘This is how we decided to minimise dust formation.
The dust often contains residues of pesticides and treatment agents, and as more and more information is becoming available about the potentially harmful long-term
consequences of this, we want to avoid the breathing in of dust as much as possible in future’, says Henk’.
Minimal footprint
‘We discussed our requirements with Prinsen and DT Dijkstra and they came up with several solutions, all workedout in 3D blueprints. This enabled us to form a clear picture of the pros and cons of the solutions proposed.
We had several sessions with DT Dijkstra to discuss the possibilities, and the ensuing modifications were consistently processed in 3D blueprints.
We liked this approach, which gave us the opportunity to make the right choices’.
Eventually, the brothers opted for a 5 bunker configuration, with the RT 2/5 grading machine installed above it.
This machine features a frequency control for setting the shaking speed, plus a hydraulic sieve clamping system which enables a fast and easy change of sieves.
A distributor conveyor was installed behind the grading machine.
The use of adjustable guidances facilitates various choices for the use of the bunkers.
A hedgehog conveyor leading to the grading machine was also installed.
Henk’s verdict: ‘Thanks to this installation and its effective grading method we are ready for the future.
We are very happy with the collaboration with DT Dijkstra, and we expect this relationship to continue for many years’.
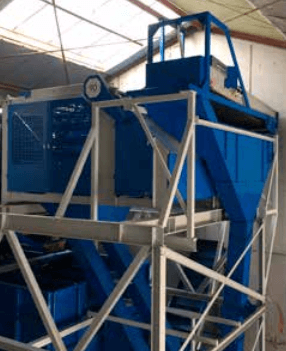